Chains represent an extremely adaptable class of device
Chains represent an extremely adaptable class of device. As part of a vast array of haulage solutions, chains allow to flexibly lift, move and lower loads of various shapes and dimensions.
Their functionality and reliability are further expanded by coupling them with lifting beams. Used for safety, they supply an effective backup to other forms of couplings, such as towing drawbars.
Thanks to their linked nature, chains can perfectly adapt to both standard and non-standard load and component shapes and sizes, integrating well within the overall rigging setup. While mass-produced chains are widely available for ordinary, lighter loads, specialised chains may be required when dealing with unusually heavy weights or exposure to heat or chemicals.
Chains that need to satisfy such tough requirements are, in fact, often found in specialist applications, such as mining and mineral processing, metallurgy, timber, specialised lifting and marine operations, to name a few. In the latter case, they find their use in anchoring, lifting and towing operations both at sea and in port.
As they constitute an element of the load path (directly or as backup), chains can occasionally be subject to rigging failures. When failures do happen, they tend to do so ruinously and without warning. This is why Reliance Hexham chains are manufactured from a combination of material types to ensure energy at failure is absorbed, rather than catastrophically failing.
Along with other lifting devices, chains need to be thoroughly checked and tested on a regular basis, Australian Standards issue strict regulations in this regard so as to promote the safety of all personnel and equipment on site.
The relevant Australian standards specifying the requirements for chains include:
- AS 3751- Underground mining – Slope Haulage – Coupling, Drawbars and safety chains,
- AS 2321- Short-link chain for lifting purposes
- AS 3637 – Underground Mining – Winding suspension equipment – Shackles and Chains
- AS 3775 series – Chain slings for lifting purposes – Grade T (80) and V (100)
- AS 3776 – Lifting components for Grade T (80) and V (100) Chain Slings
Two aspects particularly relevant for chains are testing and inspection. Proof load testing is compulsory after manufacture, when load-bearing components have been replaced and when tags are missing.
This test verifies that the device can withstand a designated load level securely and without suffering any unacceptable deformation.
Proof load tests are followed by magnetic particle examination to exclude imperceptible fatigue cracks that may have formed during the test.
The second requirement for chains is a regular inspection. Each lifting device that is in service needs to be visually inspected prior to each use or shift by a competent person.
Lifting devices that need to be inspected include chains involved in lifting, flexible steel wire rope (FSWR), shackles, synthetic slings, hooks and catches.
Periodic inspection interval requirements range from yearly to monthly, depending on the number of lift cycles that the device goes through, where a lift cycle is defined as lifting and then lowering a load once.
During an inspection, attention should be paid to any cracks, the presence of chemical damage (such as stains or burns), gouging, or other deformations.
Worn components are measured for wear. Proper cleaning and maintenance are also essential and allow to extend the service life of lifting components considerably.
Chains
Our commitment to our customers allows us only to employ the highest quality materials; the same care goes into delivering lifting solutions bespoke to the clients’ requirements.
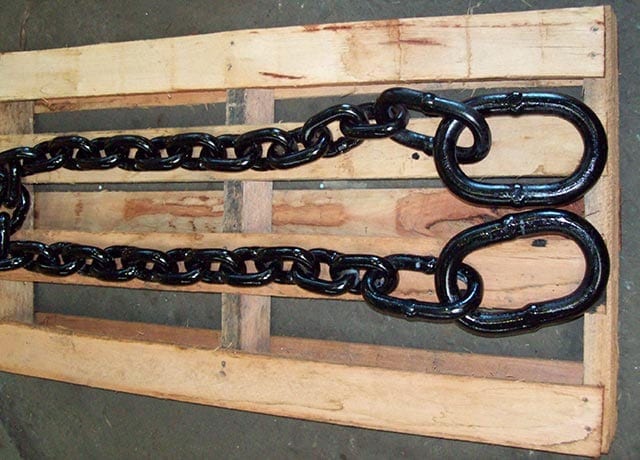
In today’s times of increasing workplace safety, you cannot afford to use second-rate lifting and safety equipment.
Our fully integrated engineering and manufacturing facilities mean that we can take care of your project starting from design to production and testing (available both in-house and on-site with minimal impact on your daily operations).
All specialised chains are made in our workshop by our qualified tradespeople, applying rigorous quality controls at every step of the process.
Each item is manufactured to current Australian Standards and issued with NATA certification in accordance with out scope of accreditation.
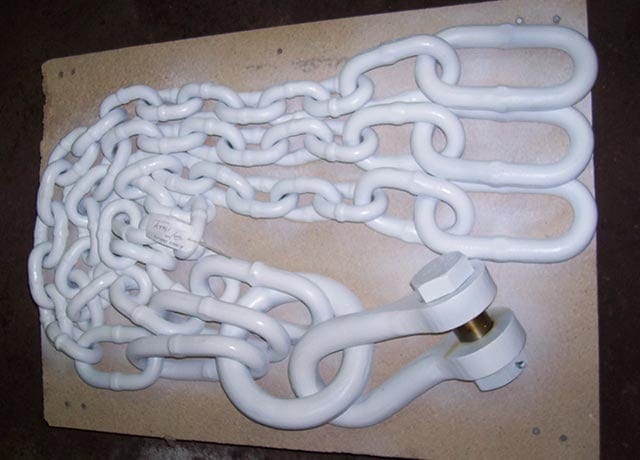
We supply chains and chain components for a wide selection of industries across Australia, including mining and mineral processing, timber, steel and aluminium processing, marine and specialised lifting, industrial lifting, and specialist applications.
Our lifting range includes:
- Suspension chains
- Safety chains
- Kibble chains
- Specialised chains
- Chains slings
- Lifting beams
- Attachments
- Hooks
- …and other accessories to customers’ own requirements.
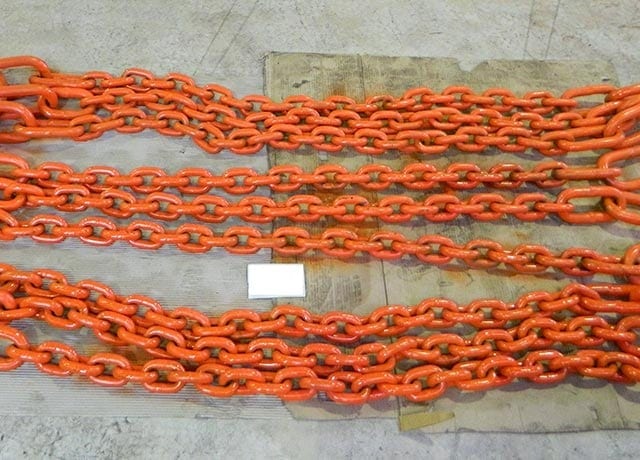
The scope of our projects may include:
- Item Assessment
- Design
- Replacement of Parts
- Repair of Parts
- Butt welding
- Heat Treatment
- Hardness Testing
- Proof Load Testing
- Dimensional Check
- Function testing
- Magnetic Particle Examination
- Protective Coating
- Final Inspection
- NATA Certification
Reliance Hexham can manufacture a range of safety and lifting chains, in numerous different sizes to suit our customers’ unique needs, utilising our butt welding system.
Please do not hesitate to contact our team for expert advice on your specific application.