Sheaves are instrumental to keeping safety high and costs low, optimising equipment performance and increasing its longevity
The efficiency and safety of the wire rope and the traction sheave is determined by the coefficient of friction between the wire rope and the lining. Sheave wheels, or simply sheaves, minimise such friction and so decrease the wear of lifting and pulling equipment over their service life.
In fact, sheaves are instrumental to keeping safety high and costs low, optimising equipment performance and increasing its longevity.
Factors that can impact on the friction coefficient between the wire rope and the sheave lining include wire structure, load weight, the speed with which the wire moves, lubrication if any, and environmental conditions, such as temperature and moisture.
Corrosion is the enemy of any metal equipment, hence the latter should be appropriately designed (water-proofing, finishing), particularly in a salt water environment.
A multiplicity of designs have been engineered over the years to tackle the different challenges presented by pulling and lifting operations, guaranteeing an optimal coefficient of friction between the sheave and the wire rope.
Suffice it to say that sheaves play a critical role in the processes of industries as diverse as construction, transportation of men and material within mines (vertical and sloping access shaft mining), steel rolling mills and metal processing.
Sheaves carry out a number of functions, from pulling and lifting, to laying underwater pipes and cables.
Even the sturdiest of sheaves require maintenance and careful inspection, as regulated by Australian Standards in AS 3785.7 – Underground mining – Shaft Equipment – Sheaves and AS 2089 – Sheave Blocks for Lifting Purposes.
Just like any other equipment involved in lifting operations, sheaves must be inspected before each use by a competent person. Issues to look out for include wear, fatigue cracks, corrosion and the presence of foreign matter which may impact friction. Periodic greasing may also be required, depending on the application.
Detailed visual checks should be scheduled on a monthly basis. Moreover, Australian Standards lay out the requirements for sheaves testing and certification.
Mandatory proof load testing before service serves to certify that a sheave is fit to stand its standard workload limit with a safety factor of 1.2 or higher.
On-site non-destructive examination techniques, such as magnetic particle testing, should also be regularly implemented to locate fatigue cracks before they become a safety issue.
Sheaves Services
Reliance Hexham has been involved in work with sheaves for many years and can design, manufacture and overhaul a range of sheave styles and configurations.
Our engineering department has extensive experience in designing, manufacturing and refurbishing of head sheave assemblies for customers in Australia and overseas.
At the same time, our team of qualified tradespeople have over 165 years of industry experience between them, and is well equipped to understand your daily challenges and operational needs.
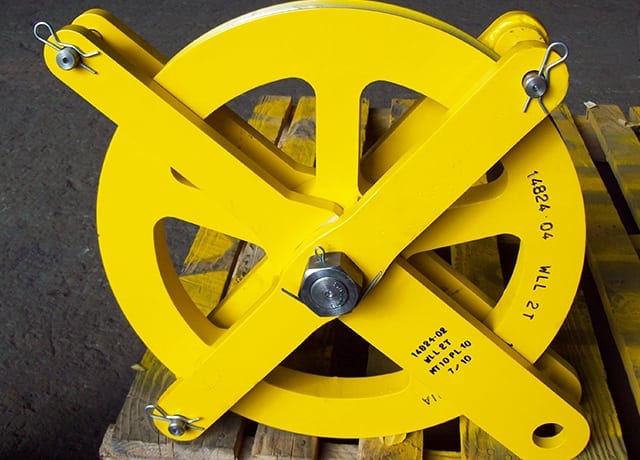
To guarantee the highest quality of our products, every step of the process, from design to testing, including material selection and manufacturing methods, is carried out with professionalism, monitored and documented.
All our production and repairs by way of welding are examined using non-destructive testing methods, such as magnetic particle inspection.
We are able to deliver on niche, high-speed and high-load hoist requirements in a variety of sheave sizes.
Projects we have delivered comprise the following styles:
- Double down sheaves
- Deflection sheaves
- Compensating sheaves
- Sinking sheaves
- Classical (conventional) sheaves
- Sheave blocks
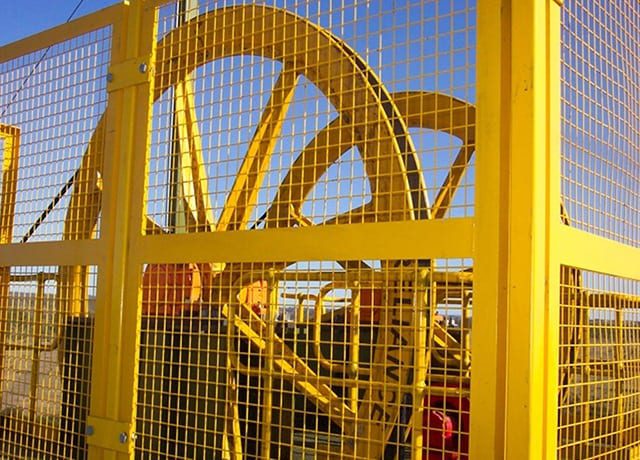
Applications that we have experience working within the past include the following:
- Slope haulage
- Vertical shafts
- Aluminium and steel processing
- Construction
- Marine industry and port services
- Specialised lifting
To guarantee the highest transparency and utility from our sheaves, design and manufacture information provided to the customer includes:
- Sheave mass
- Sheave Inertia
- Angle of wrap
- Fleet angle
- Rope groove wear limit
- Calculated bearing life
- Static balancing
- Maintenance regime
Testing Facilities
In addition, we provide testing facilities accredited by NATA, National Association of Testing Authorities, on-site or on our premises as required. We are able to carry out non destructive testing and/or destructive testing to issue certification in accordance with our scope of accreditation
To find out more or if you have any questions, please do not hesitate to reach us by phone or email. Our personnel will be happy to provide you with professional advice for your particular application.