Excessive strain and repeated heavy use of equipment may cause dangerous discontinuities to form which, with time, can lead to irreversible fatigue cracks and even full breakage.
Flaws can also develop during the hardening process of material if this is carried out incorrectly. In order to pre-empt costly and hazardous incidents, a magnetic particle test is recommended.
Also known as magnetic particle inspection or MPI, this is a non-destructive type testing (NDT) implemented to discover cracks and other discontinuities on or near the surface of ferromagnetic and electrically conductive materials, and is one of the most used techniques to this end.
The magnetic particle testing procedure is a relatively straightforward method, although it requires both attention and experience so as to avoid false negative results.
The first step of the process consists of evaluating the test subject, which is then prepared for inspection, opting for a cleaning process that does not adversely affect its characteristics.
The test is in fact classified as an NDT since it does not cause unacceptable deformation of test pieces. After the cleaning, the appropriate test method, either white contrast or fluorescent, is selected .
Next, the process involves using AC or DC yokes to magnetise the part under test, before application of the magnetic particles themselves. The specimen can be magnetised either locally or as a whole, with the magnetic poles placed between 7cm and 25cm from each other.
Key to a correct evaluation is the activation of the magnetic charge so that they are immediately free to be attracted to any leakage fields on the test piece.
Additionally, it is imperative to make sure that 100% of the component’s exterior is examined so as not to miss any flaws.
After the element is demagnetised, it is time to visually inspect it for any irregularities.
If there is an exterior or near-surface fracture, the magnetic field will be altered by a local flux leakage at the site of the damage, creating a visible indication of discontinuities on the component’s surface.
The nature and size of the discontinuity can be roughly estimated by the amount, density and shape formed by the clustered magnetic particles.
An inspection by means of magnetic particle testing is suitable for most equipment and pieces composed of ferromagnetic material. Ideal conditions for testing are as-welded, as-cast, as-rolled or as-forged and smooth blasted surfaces.
Industry applications range widely and comprise all those businesses involved in lifting, moving or otherwise handling substantial weights as part of their operations: mining, equipment manufacturing, metal processing and materials handling to name a few.
While law often mandates magnetic particle testing frequency, it is recommended to periodically carry out this inspection so as to avoid unpleasant surprises. Additionally, MPI is a valuable instrument to reveal manufacturing or processing defects, for instance after heat treatment.
Magnetic Particle Testing
Reliance Hexham offers expert magnetic particle testing services thanks to the extensive experience of our skilled team of qualified technicians. Our laboratory is accredited to ISO 17025 – General Requirements for the Competence of Testing.
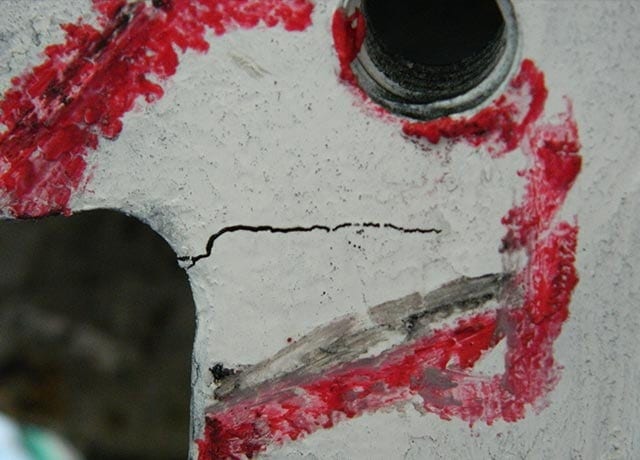
We have facilities to carry out MPI at our premises as well as on-site as required by the customer.
All testing carried out by Reliance Hexham to our scope of accreditation and traceable as per our quality assurance certification.
Our Level 3 & Level 2 AINDT accredited magnetic particle technicians are approved for multi industrial sectors and testing is carried out in compliance with AS 1171.
Our comprehensive examination is carried out quickly and efficiently, with minimal impact on your daily operations.
It is the minimum standard within our organisation to conduct magnetic particle testing on all ferromagnetic items that we have manufactured or repaired.
In addition to regularly testing equipment produced in-house, Reliance Hexham has for many years supplied MPI services to a variety of clients within the specialised lifting, manufacturing, materials handling and mining industries, among others
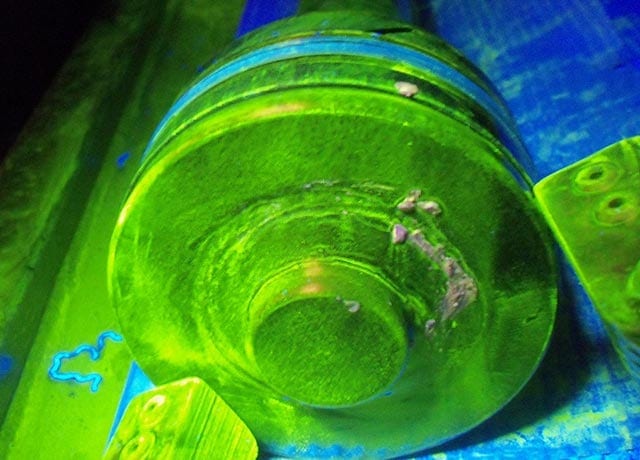
Common test subjects include cranes (see our page dedicated to Crane Audits), hooks, elevated work platforms, forklift attachments, QDS attachments, rope attachments, couplings and drawbars.
We also offer weld repairs and refurbishment services for equipment that is found to contain fractures, where safe to do so. Afterwards, we carry out final testing to ensure that there are no longer any discontinuities present.
An application of the magnetic particle testing method has allowed our team to discover dangerous discontinuities within a fleet of elevated work platforms, which we then re-engineered and brought back up to safe running condition.
If you have any questions or require a consultation, please do not hesitate to connect with our professional team at the contact details supplied below.